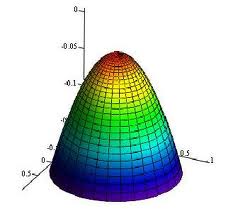
Following the customer’s request, IODA has created a parabolic mirror to focus led light. This project is called “LUX” and it is an excellent example of the potential of IODA’s factory.
Objective of this project is to channel the LED light with the highest efficiency.
This project has tree development steps:
- First – Calculation of the paraboloid curvature of the reflecting mirror and realization of the mapping of the surface, in order to process it with the freeform line.
- Second– Glass mould production (In bk7 glass), It will be an empty space for the parabolic mirror.
- Thirt – Production of paraboloid optical surface in hard resin (CR39).
Calculation of the paraboloid curvature of the reflecting mirror and realization of the mapping of the surface, in order to be able to process it with the freeform line.
A parabolic (or paraboloid or paraboloidal) reflector (or dish or mirror) is a reflective surface used to collect or project energy such as light, sound, or radio waves. Its shape is a part of a circular paraboloid, that is the surface generated by a parabola revolving around its axis.
The calculation parameters of the curvature paraboloid are based on the knowledge of the desired amplitude of the beam light and the type of LED adopted. We have used a software program developed internally by the R & D and CAD programs to create a virtual mould’s model.
Glass moulds production (In bk7 glass).
The glass mould production is also divided in three steps:
roughing and polishing of raw materials via freeform machine, polishing with a special flexible tool, and visual inspection.
.
.
.
.
.
The last stage of the production process is the polishing. It is performed with a flexible tool which can copy a parabolic surface mould.
The accuracy of the surface produced is sub-micrometric.
.
.
.
.
.
.
The product finally obtained is dimensionally controlled and the surface is examined by the viewer to ensure the required surface quality; any imperfection would increase the adhesion with the injected resin and make difficult its detachment.
.
.
.
.
.
Production of paraboloid optical surface in hard resin (CR39).
The paraboloid mould, called “Master”, is inserted into a cylindrical container and then is injected into the hard resin, which cures following a particular thermal cycle in an oven with water. The preparation of the container and the insertion of the Master takes place in a department controlled atmosphere; this prevents that the injected resin may be contaminated by external factors.
When the hard resin is cured, and the inner surface has passed a visual inspection, the inner surface must be aluminized.
The final test has been performed inside the owner’s factory, the intensity and amplitude of the light beam have been checked.
The final product has been a big success!
The creation of the parabolic mirror is an example of IODA’s production capacity.